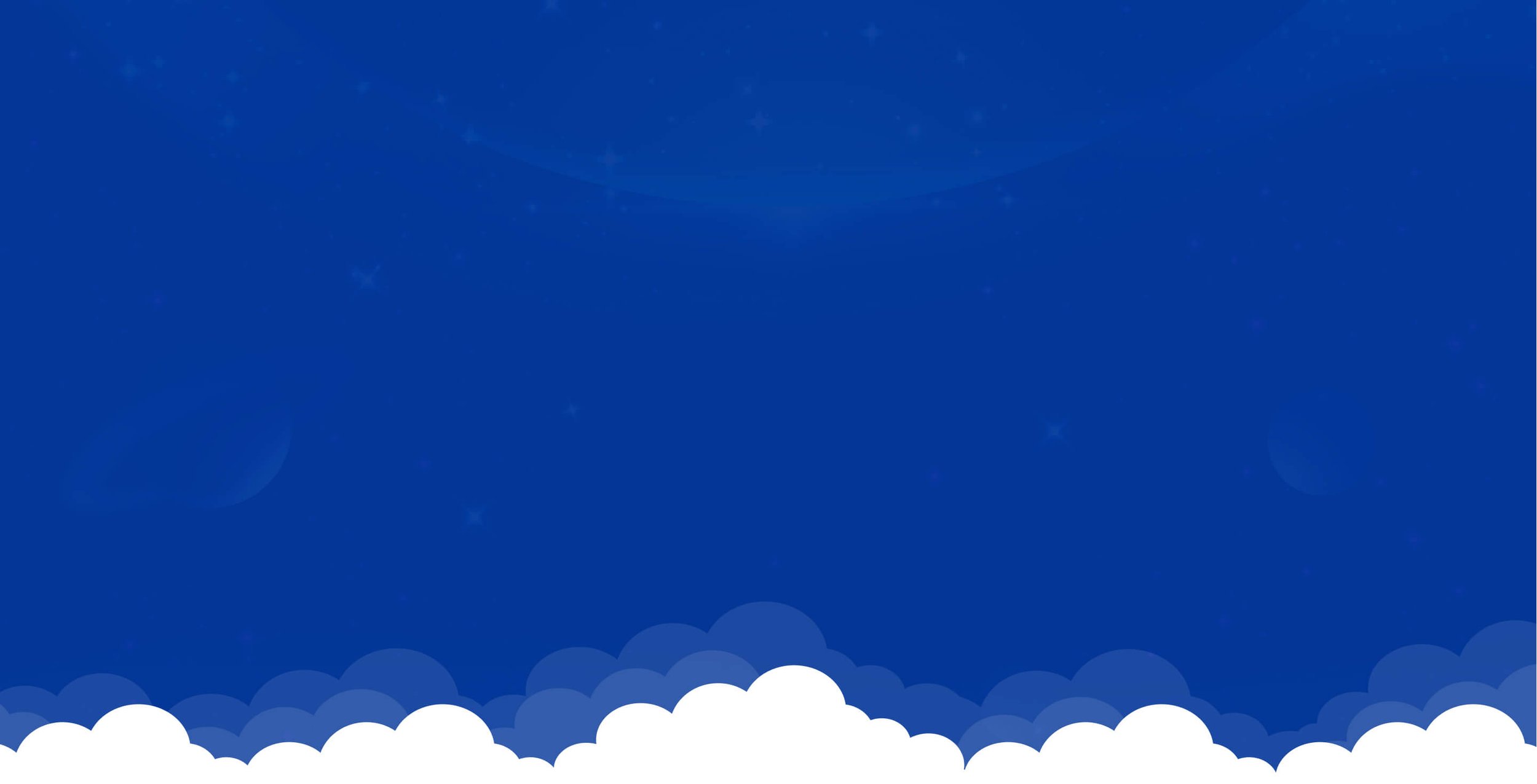
Aviation Students Test Their Knowledge With Mock Exams
Providing comprehensive online aviation mock exams under realistic conditions to test your knowledge.
Comprehensive Mock Exams & Unlimited Access
Test your knowledge with our well crafted online aviation mock exams, designed to replicate the CAA NZ examination by Aspeq. Covering a broad range of topics like meteorology, navigation, and air law, our mock exams ensure you're fully prepared for the real test. With unlimited access upon subscription, gain entry to all PPL and available CPL mock exams, with new exams added regularly, helping you practice without extra costs or time constraints.
Results Reports & Realistic Testing Conditions
Our platform mimics real exam conditions, disallowing pauses and imposing strict time limits to build stamina and focus for test day. After each mock exam, you'll receive a detailed Knowledge Deficiency Report (KDR) highlighting incorrect answers and referencing specific CAA syllabus items. This helps pinpoint areas for improvement, ensuring efficient study for your aviation qualifications.
How it Works
Create Your Account
Buy a Subscription
Select either a monthly or six-month subscription. Both plans grant you unlimited access to all 29 versions of the PPL/CPL mock exams (covering 900+ questions) throughout the subscription period.
Start Your Mock Exam
Once your subscription is active, you can begin any of the available mock exams. Each exam simulates real ASPEQ test conditions, so there’s no pause button, helping you get used to the pressure.
Get Instant Results
Once you finish your exam, the system automatically generates your results. For each passed exam, you'll see which questions you answered incorrectly, along with the correct answers and related syllabus items.
What Customers Say
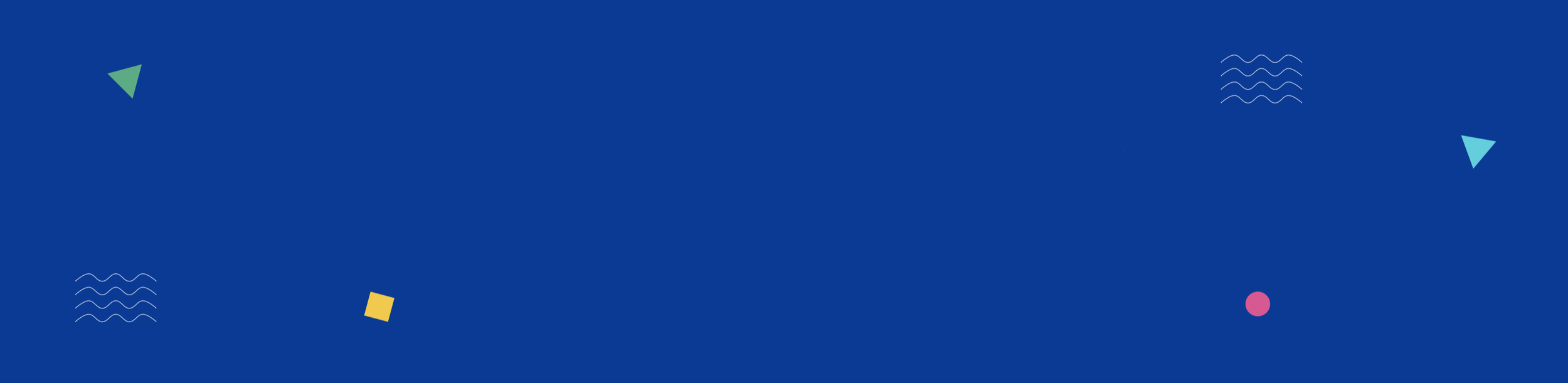
Available Mock Exams
Get unlimited access to over 1000 questions across PPL/CPL subjects with a subscription, no more one-time vouchers! Test yourself as many times as needed, with 29 mock exam versions and regular updates to keep your learning fresh.
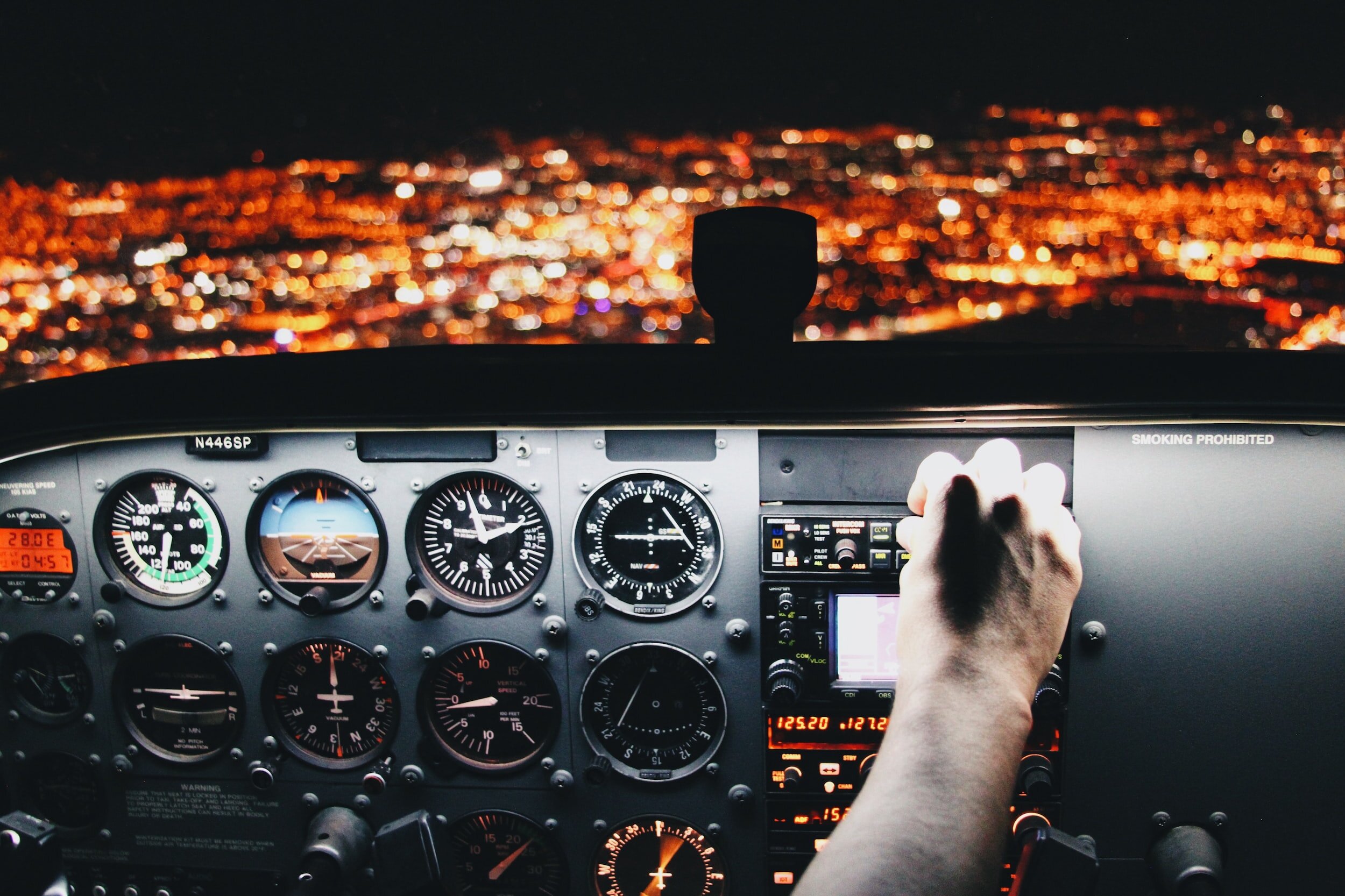
Flight Radiotelephony
Private Pilot Licence (PPL)
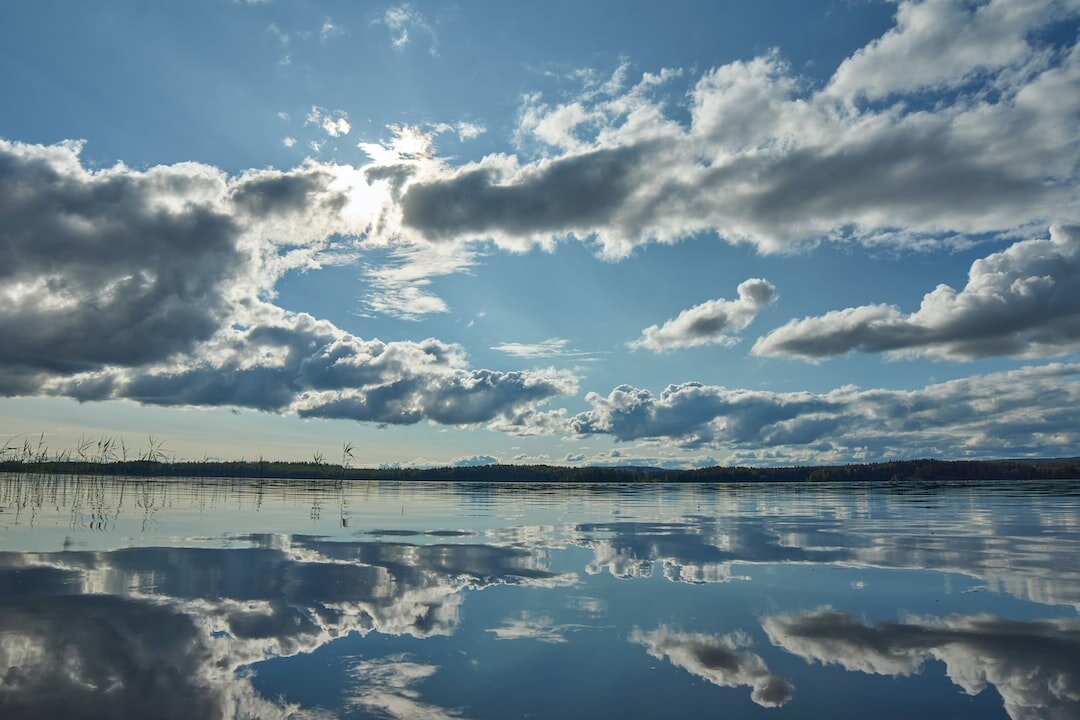
Meteorology
Private Pilot Licence (PPL)
Commercial Pilot Licence (CPL)
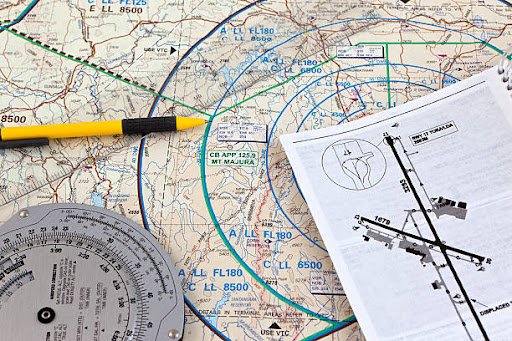
Air Navigation and Flight Planning
Private Pilot Licence (PPL)
Commercial Pilot Licence (CPL)
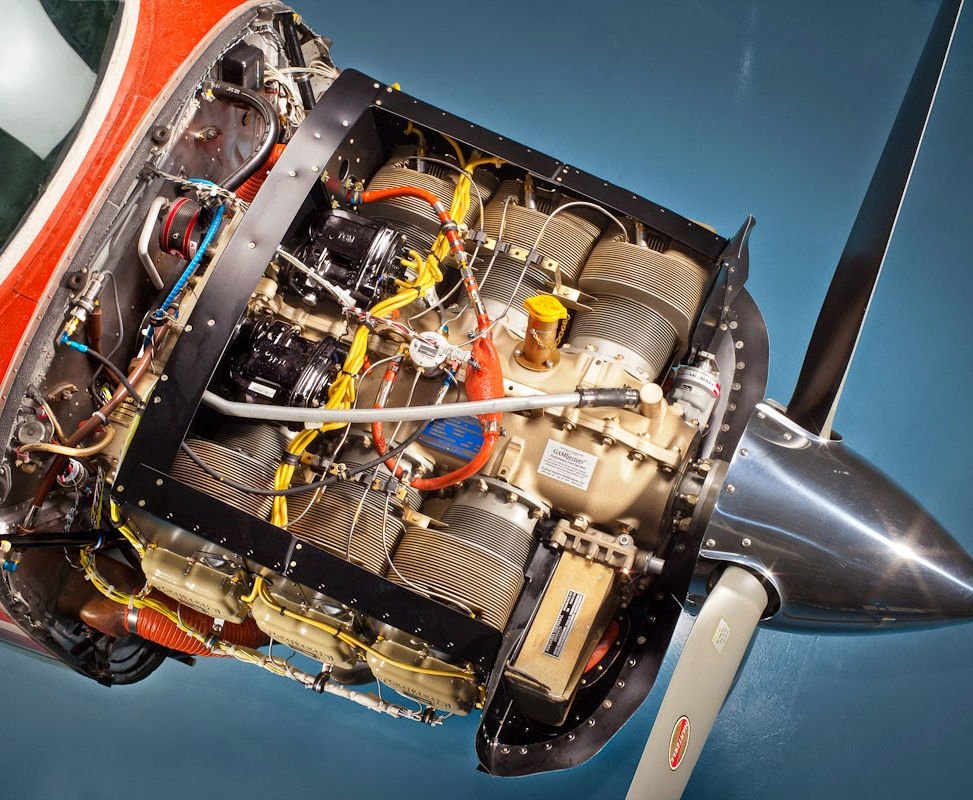
Aircraft Technical Knowledge and Principles of Flight (Aeroplane)
Private Pilot Licence (PPL)
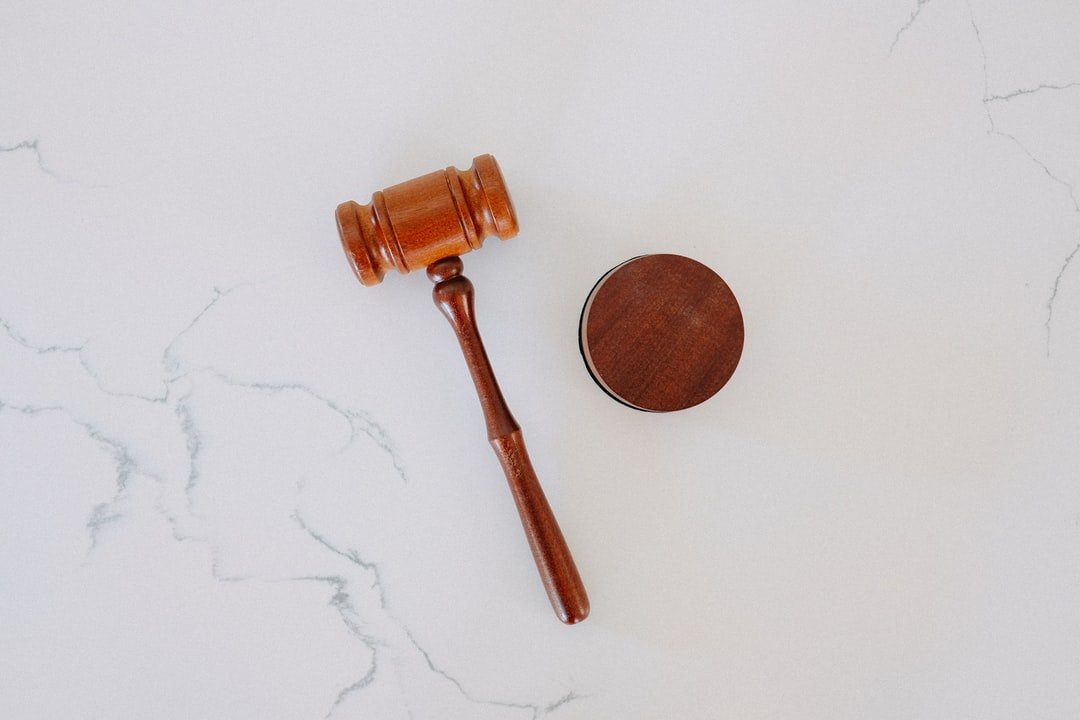
Air Law (Aeroplane and Helicopter)
Private Pilot Licence (PPL)
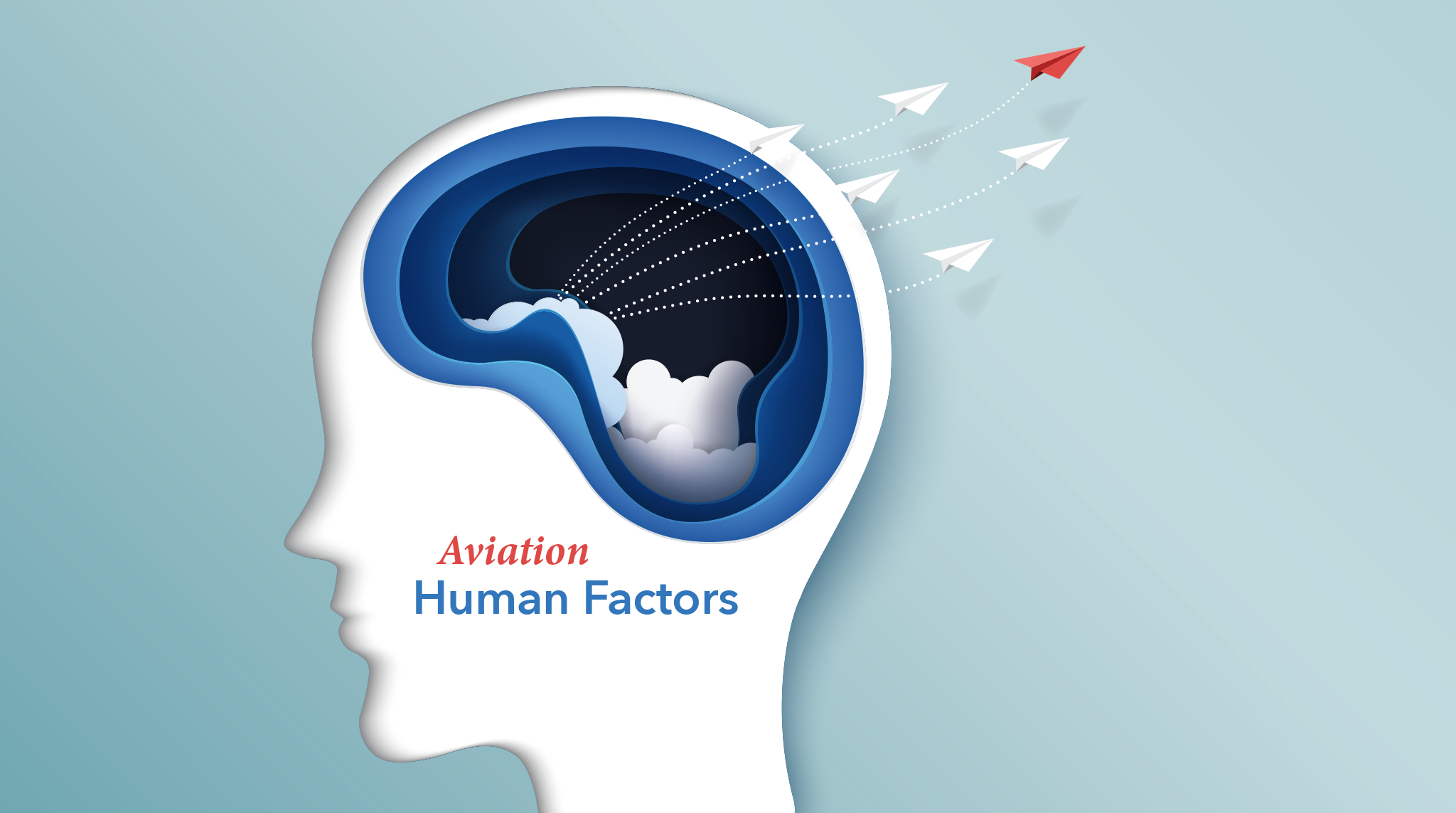
Human Factors
Private Pilot Licence (PPL)
Frequently Asked Questions
To access our mock exams, first, you need to register as a user for free on our website. Sign Up Here. After completing registration, please confirm your registration through your email (check your Junk folder).
Once registered, you can purchase a 6‑month subscription which grants full access to all our mock exams and offers discount compared to monthly payments.
With your subscription, whether it is monthly or six-monthly, you have unlimited access to all our mock exams.
Each subject offers different mock exam versions. You can retake each exam as many times as necessary, with no restrictions on the number of attempts.
Each subject comes with different mock exam versions. Every exam features a completely different set of questions. So when you retake a mock exam, you'll be exposed to new questions, providing a broader scope for testing your knowledge.
No, our goal is to simulate the real exam experience, similar to what aviation students face with NZ ASPEQ. Therefore, it’s important to be fully prepared before starting your mock exam.
However, if you need to step away, you can always restart the exam from the beginning. With your subscription, you can retake any mock exam as many times as needed.
YES, there is a time limit for each mock exam. Our objective is to closely replicate the real exam experience that aviation students encounter with NZ ASPEQ exams. The time limits for our mock exams are aligned with the actual exam constraints.
As soon as you complete your mock exam, the system automatically grades it and displays your results. You’ll see which questions were answered incorrectly, along with both your answers and the correct ones.
Additionally, each question includes a relevant syllabus study reference to help you identify areas for improvement. (HERE IS THE LINK TO AC61-3) & (HERE IS THE LINK TO AC61-5)
We greatly appreciate your feedback, as it helps us improve our services. If you encounter any errors or need clarification on any aspect of the mock exams, please fill out this form.
Once submitted, one of our instructors will review your feedback and contact you if needed.
No, we only provide mock exams to test your knowledge. When you’re ready to book your real exam, please use the link below:
Aviation Calculators
FREE and reliable aviation calculators made for kiwi pilots. Use this page to help you solve many calculation-related problems.
Start Calculating HereFlight Computer
Free online flight computer simulator to enable pilots and aviation students to learn and practice.
Start Calculating HereNavigation Flight Log
Automatically calculate True Airspeed, Heading, Distance, Ground Speed, Estimated Elapsed Time, Leg Fuel, and Fuel Remaining.
Start Calculating Here